1. 인체내의 밸브로서 본 밸브의 기능
우리 인체내에는 심장이 있고, 심장을 통하여 인체를 구성하고 있는 수십억의 각 세포에 혈관을 통하여 끊임없이 영양분을 공급함으로써 생명을 유지하는 것이다. 혈관을 통하여 흐르는 유체는 혈액이고, 혈액은 인체 내의 핵심장기인 심장이라는 펌프를 통하여 인체 내의 각 기관과, 그 안의 각 세포에 영양분을 공급하고 다시 회수되는 사이클이다. 따라서 심장은 펌프를 담당하는 근육과, 이를 각 기관에 보내고 회수하는 과정에서 어떠한 착오도 없이 완벽하게 정해진 프로세스를 가져야 한다.
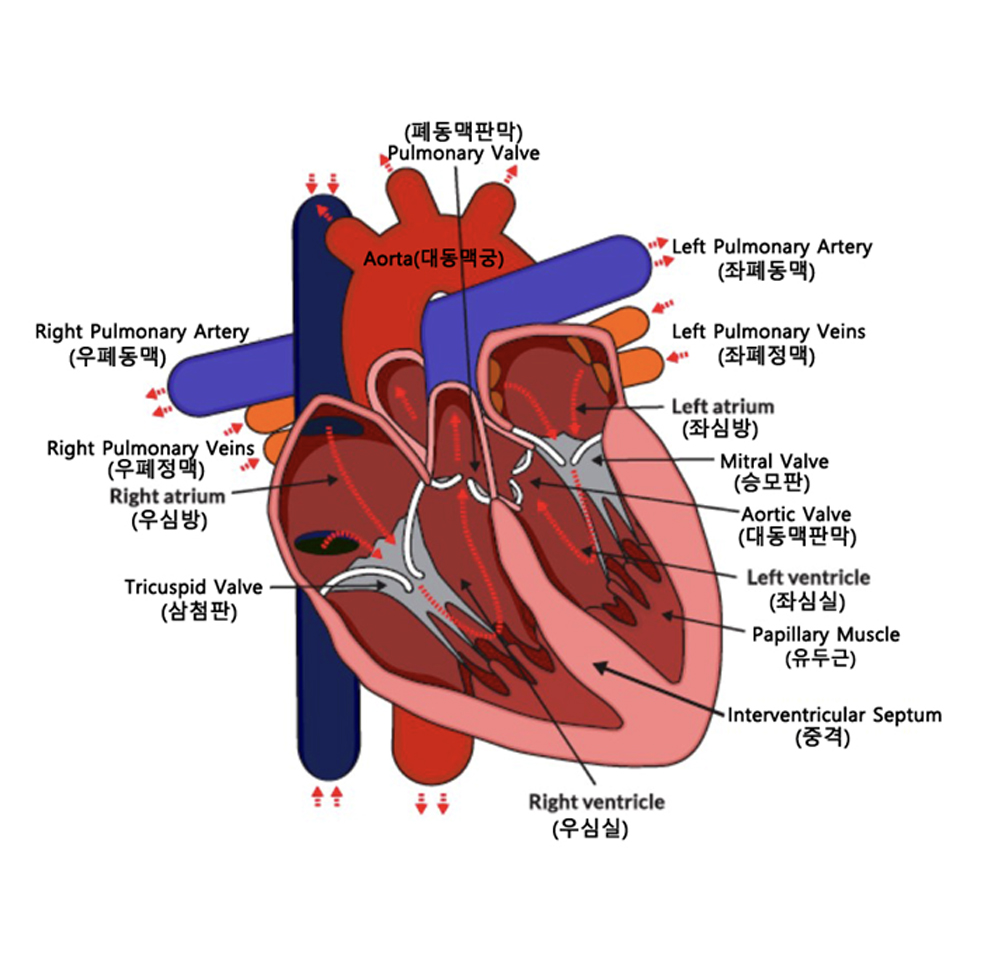
심장에는 그림에서 보는 바와 같이 각기 우심실과 우심방이 체크밸브로 혈액 의 공급방향을 제어하고 있으며, 역시 좌심실과 좌심방도 체크밸브로 혈액 흐름의 방향성을 항상 일정 하게 한다. 이들 4개의 체크밸브는 공학적 으로는 Flapper형 체크밸브이다. 마찬가지로 프로세스 모든 과정 에서도 유체가 존재하는 한 펌프와 배관, 그리고 이들을 프로세스에 맞도록 제어하는 밸브가 필수적임을 알 수 있다.
2. 일상에서의 밸브
우리의 일상적인 생활을 유지시켜주는 의식주는 우리가 살아가고 있는 동안 당연한 기본권과 같은 것이다. 현대에서는 이들 의식주의 삶에서는, 또는 좀더 나은 생활을 위하여 의식주의 수준은 과거에서 보다 더욱 크고, 아름답고, 편리하고 체계적이어야 한다. 이를 위하여 인간은 특히 산업혁명 이 후에서는 의식주와 관련한 관련 산업이 크게 발전하였다. 특히 2차 산업혁명기간동안 화학공업, 석유공업, 전력산업과 같은 기본적 산업설비가 장치산업이라고 할 만큼 규모가 커지게 되었다. 이들 장치산업을 통하여 생산된 제품들은 최종 소비자들의 의식주에 대한 기대를 충족하게 되었다.
이들 장치산업에는 실질적 제어장치로 밸브를 제외하면, 각 단계별로 세부적이고 정밀한 프로세스의 제어가 불가능하다. 밸브는 이들 장치산업의 최종적인 제어장치일 뿐만이 아니라 장치와 장치를 연결하고, 수송하고, 저장하고, 가공하고, 분배하는 전 과정의 제어요소로서 없어서는 안 될 중요한 요소이다. 따라서 어느 산업분야를 막론하고 밸브가 없는 경우는 없다. 또한 이들 장치산업이 기술발전에 따라 효율화를 추구하고, 생산성을 높이기 위하여 유체가 갖는 핵심 물리적 파라미터인 온도, 압력, 유량들의 제어요소들도 다양화와 고도화는 물론 거대화와 고에너지화 되고 있기에, 밸브 또한 이에 발 맞춰 발전해 왔다. 즉, 밸브는 우리 생활의 중심에 자리잡은 의식주에 대한 요구사항을 음지에서 지원하는 중요한 기기가 되었다. 지금의 산업은 장치산업이기 때문에 인체의 각 세포에 영양분을 공급하는 심장과 혈관처럼 밸브와 파이프로 구성되었다고 볼 수 있을 만큼 밸브의 역할과 그 비중은 크다. 이 책은 우리 일상생활에서 사용하고 있는 수도물의 제어를 위한 수도꼭지나 소화전의 밸브, 도시가스 배관에서의 가스 차단 볼밸브 등, 생활과 직접적인 연관을 가진 가정용이나 설비용 밸브를 대상으로 하지는 않는다. 그러나 우리 생활의 곳곳에는 물∙가스의 차단이나, 유량조절의 목적으로 설치 운용됨을 알 수 있다.
3. 밸브의 정의
밸브는 유체를 수송하는 장치의 배관 시스템에 설치되어 유체를 차단 또는 조절하는 밸브류의 총칭이다. 유체를 흐르게 하거나, 멈추게 하거나, 조절을 하기 위하여 유체흐름을 개폐하거나 개폐의 크기를 조정할 수 있는 운동기구를 가진 기기를 종합하여 부르는 것. 유체의 제어적인 측면에서는 시스템에서 요구하는 제어 중, 가장 최종에서 제어를 담당하는 것으로 밸브를 정의한다.
4. 밸브의 분류
밸브를 체계적으로 분류하기 위해서는 밸브의 구성재질이나, 고온 고압의 정도에 따른 압력-온도의 기준, 또는 주로 사용되는 산업별 혹은 밸브 구조에 따라 분류를 할 수 있지만, 사용분야가 너무 중첩되는 경우가 많아 체계적인 분류가 어렵다. 따라서 이 책에서는 재질의 종류, 주로 사용되는 산업분야와 밸브 구조에 따른 분류를 시도한다.
(1) 수동조작 밸브구성
수동 조작의 밸브는 조작의 방식에 따라 선형동작(Linear Sliding Motion)과 90도 회전동작(Quarter Turn)으로 구분되고, 이에 따라 밸브 종류/유형을 구분할 수 있다.
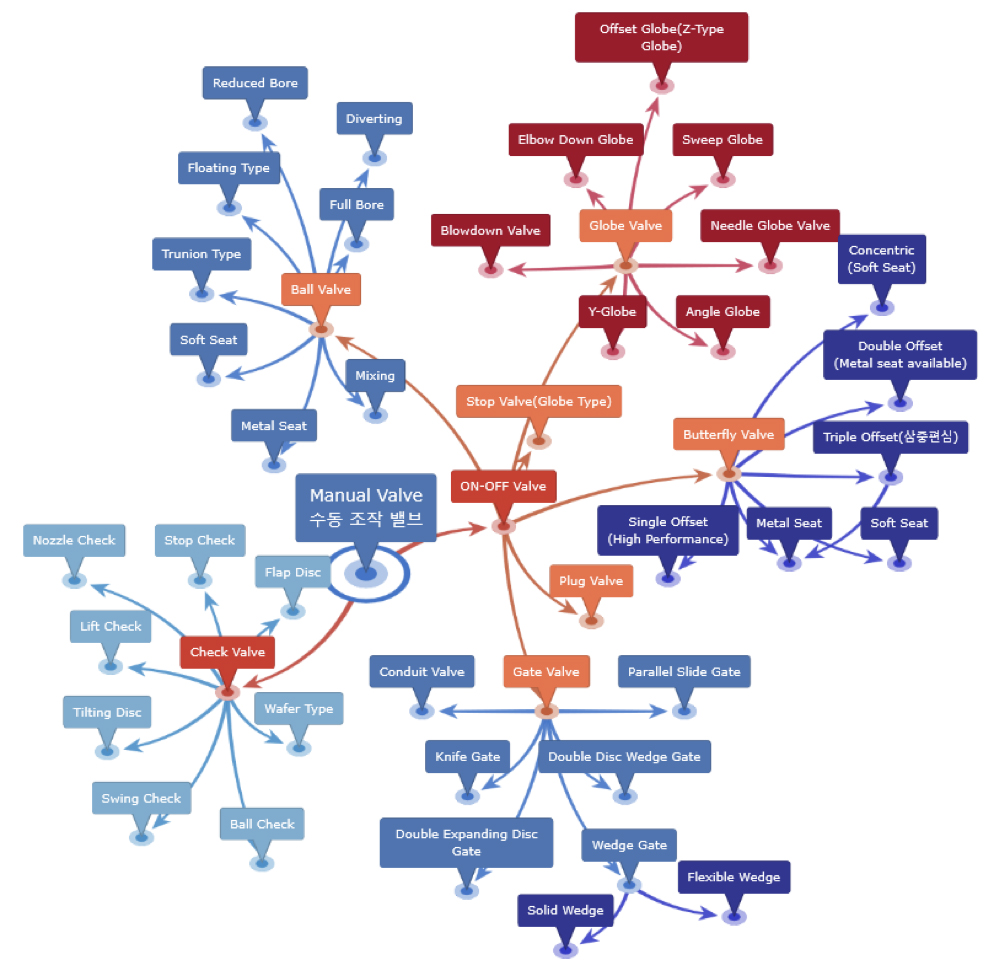
수동 조작 밸브 및 체크밸브 종류별 그룹
(2) 자력식밸브(Self Operated Valves) 구성
자력식 밸브는 외부의 조작없이 유체의 흐름이나, 압력에 의하여 스스로 정해진 동작을 하는 밸브를 총칭하는 것으로, 유체의 흐름에 있어 역류(逆流, Reverse Flow)을 방지하여 시스템의 안정적인 운전을 도모하는 체크밸브 (또는 역류 방지 밸브, Non Return Valve)와 시스템의 압력이 설정 값보다 크게 되면 밸브가 동작하여 시스템의 압력을 안전범위로 복귀하도록 하는 안전밸브 및 릴리이프 밸브가 있다. 이외에 시스템 자체의 유체 특성 즉, 압력, 유량(유속), 온도를 밸브 자체의 압력손실 기능을 이용하여 스스로 조정하는 조정밸브(Regulating) 밸브가 있다. 조정밸브는 실제 산업현장에서 익숙하지 않은 용어이어서 이 책에서는 레귤레이팅 밸브라고 호칭한다.
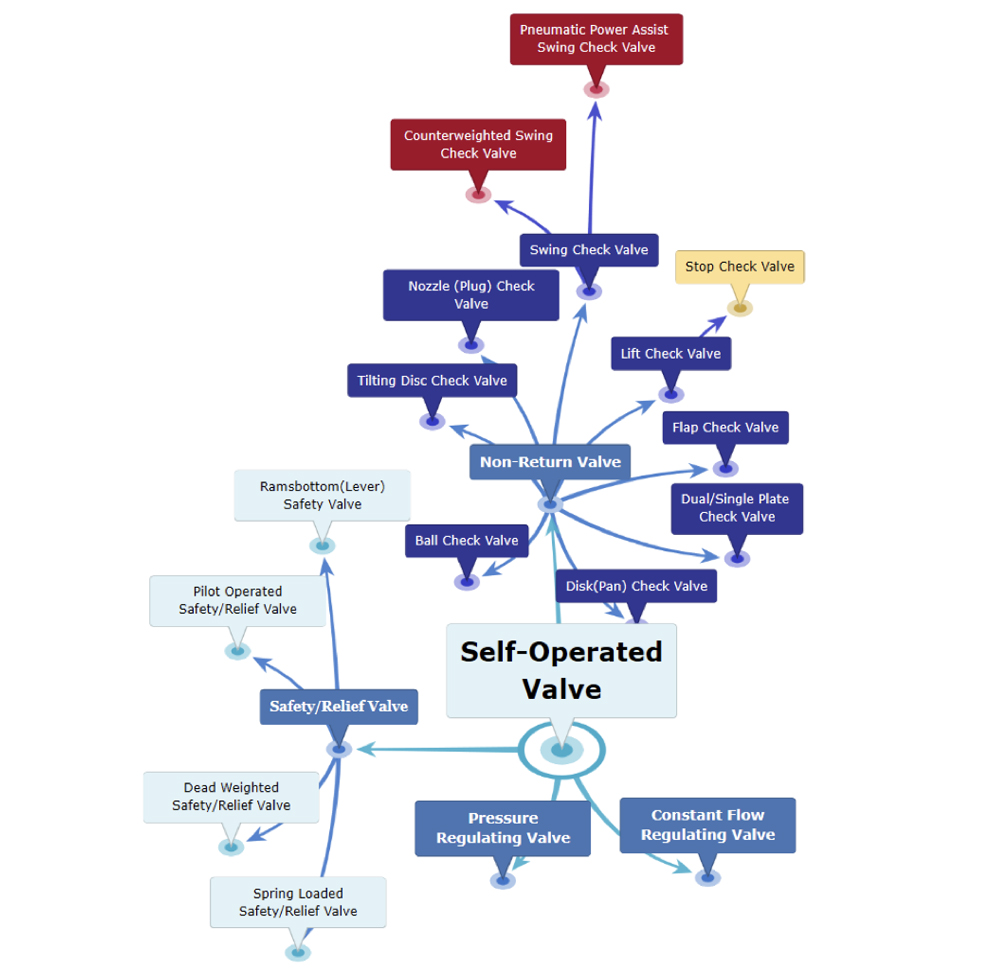
자력식 밸브(Self Operated Valves) 그룹
제어밸브의 경우는 시스템의 제어목적에 따라 압력(PCV), 유량(FCV), 온도(TCV) 및 수위 레벨(LCV)이 대부분이다. 제어밸브는 제어부에서 신호를 받아 밸브 동작에 필요한 힘을 전기나 공압, 유압력을 이용하여 제어하는 것으로, 시스템 내의 제반 물리적 상태를 감지 계기로부터 전기적 제어신호를 받아 이를 제어부에서 시스템의 운전 상황에 맞추어 연속적으로 조절하는 밸브이다.
(3) 레귤레이팅 밸브
전형적인 자력식 밸브의 하나인 레귤레이팅 밸브를 제어 목적별로 구분하면 다음과 같다.
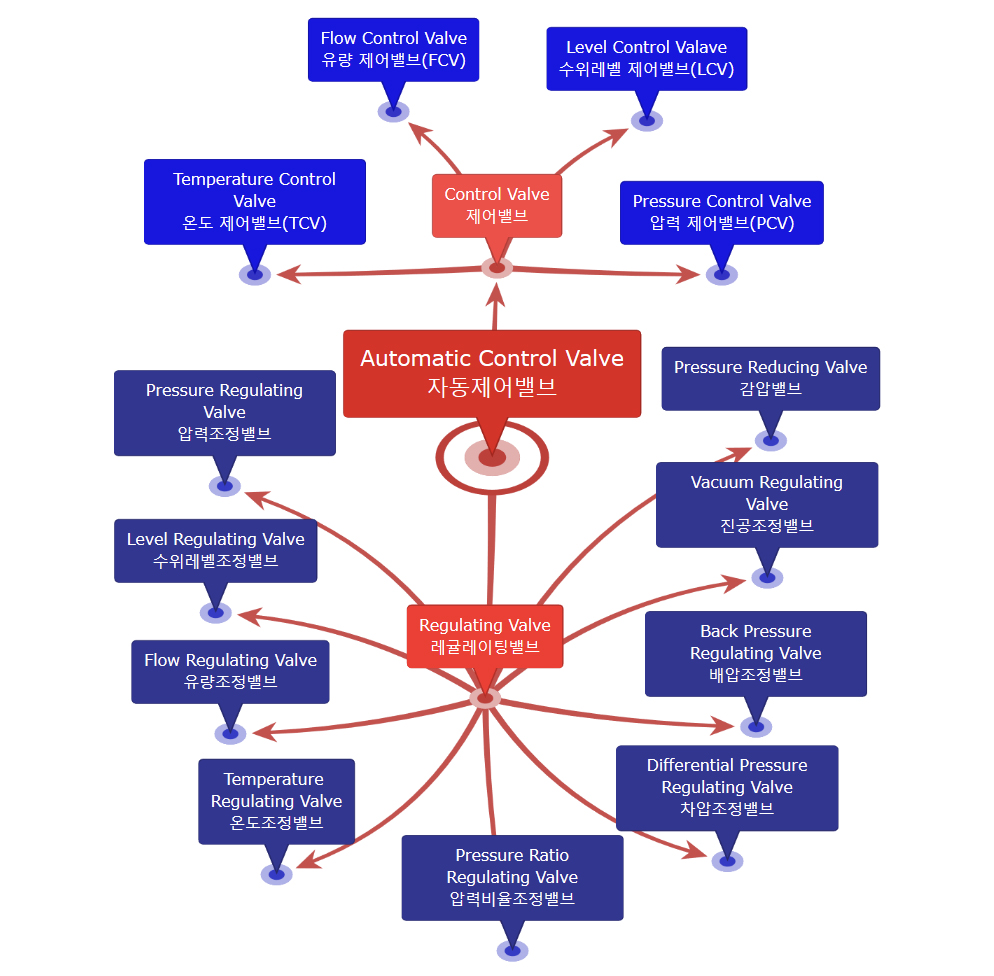
자동 제어밸브의 레귤레이팅밸브 그룹
(4) 동력 구동장치부착 밸브(Power Operated Valve) 구성
밸브의 구동을 전기 모터, 공압 피스톤이나 공압 구동 모터, 또는 유압의 힘을 이용하여 밸브를 개폐하거나 개도를 조절하는 밸브를 통칭하여 동력 구동장치 부착 밸브, 또는 동력 구동밸브라고 한다.
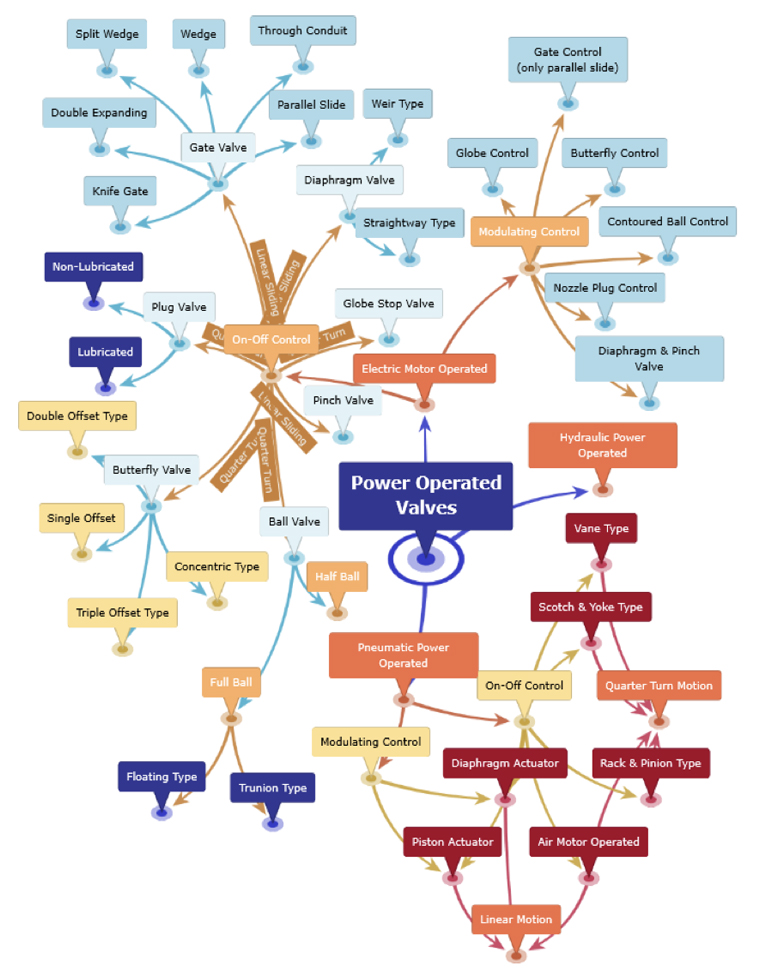
구동장치 부착 밸브(Power Operated Valves) 그룹
동력 공급원에 따라 전동구동(Electric Motor Operated Valve, MOV), 공압인 경우 공압구동(Pneumatic Power Operated Valve, POV)이라고 한다. 동작방식에 따라 선형동작과 90도 회전동작이 있으며, 또한 밸브 개폐 동작과 조절 동작으로 구분할 수 있다. 동력원(동력원, Power Source)에 따라 매우 다양한 구동장치가 개발되어 있으며, 그 형식 또한 다양하다.
(5) 밸브조작 방법에 따른 분류
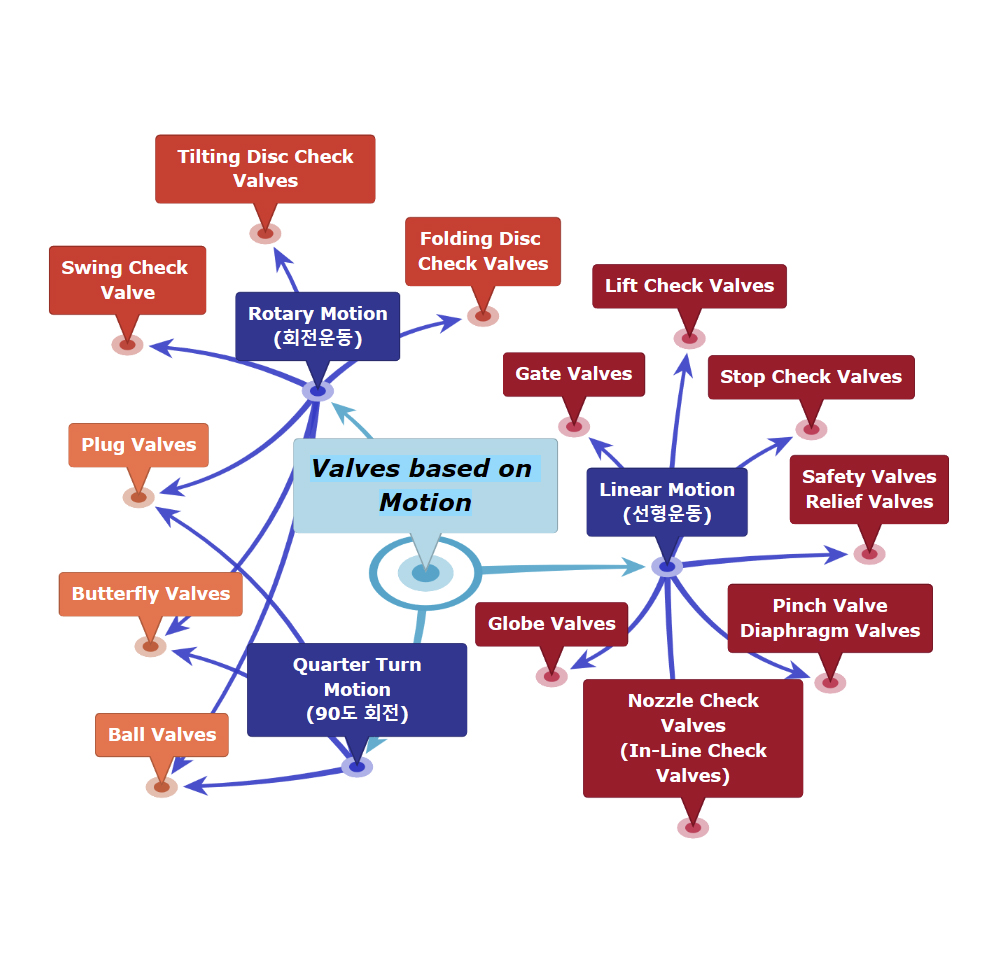
(6) 밸브재질에 의한 분류
밸브 재료는 압력을 직접적으로 받는 압력유지 부품인 밸브 몸체와 밸브 본닛의 재료로 구분하면 다음과 같다.
- 비철금속 – Non Ferrous Steel, (청동, 황동, 알루미늄, 모넬 등의 비철합금)
- 주철 – Cast Iron, (주철, 가단주철, 구상 흑연 주철 등)
- 주강 – Cast Steel, (저합금강 포함)
- 단조강 – Forged Steel, (저합금강 포함)
- 스텐레스강 – Stainless Steel, (주조, 단조를 포함)
- 초합금강 – Super Alloy Steel, (주조, 단조를 포함)
ASME B16.34 Table 1에 의하면 주조 및 단조로 밸브의 압력 유지 부품에 사용할 수 있게 승인되어 있는 밸브 재료는 2017년 기준 49종이며, 이중 주조와 단조 사양으로는 다음 테이블과 같이 요약된다.
재료구룹 | 구룹 수 | 주조 사양 품목수 | 단조사양 품목수 | 주요 재료 통칭 |
구룹 1 | 18 | 15 | 17 | 탄소강, 저온강, 저합금강, 내크리이프강 |
구룹 2 | 12 | 19 | 19 | 오스테나이트 스텐레스강, 듀플렉스강 |
구룹 3 | 19 | 6 | 24 | 수퍼 알로이강, 인코넬, 인코로이 |
밸브 주조/단조 재료 사양 품목 요약
(7) 용도에 의한 분류
밸브의 용도별 분류는 크게 구분하여 건축 설비용, 상하수도 설비용, 프로세스 플랜트용, 선박용, 기계 및 운반기계용으로 구분하고, 이를 보다 세분화하면 다음과 같이 분류할 수 있다.
- 건축설비용(가스, 냉난방, 공조 등)
- 상하수도용
- 농업용(관개, 낙농.축산)
- 일반 기계용
- 화학공업용(식음료, 섬유, 연료, 의학, 생활화학)
- 발전용(수력, 화력, 태양열 발전, 원자력등)
- 석유화학공업용(정유, 석유 정제, 석유화학)
- 의료용
- 선박용(수중, 수상, LNG선 등)
- 가스공업용(석탄, 석유, 천연가스 등)
(8) 밸브구조에 의한 분류
밸브의 기능적 측면에서는 단순히 개폐 동작만을 요구하는 경우와, 배관 시스템의 제어 목적에 맞게 기능적 역할을 하는 최종 제어요소로서 밸브인 제어밸브로 두 개의 기능이 있지만, 밸브 구조로 분류한다면 좀 더 복잡하게 분류하여야 한다. 첫째는 선형 슬라이딩을 하여 유체 흐름을 제어하는
밸브 구조와 회전으로 흐름 제어를 하는 밸브 구조, 그리고 시스템 내부로 흐르는 유체의 운동에너지를 스스로 이용하는 자력식 밸브 구조로 나눌 수 있다. 힘의 분류에 의해 조작되는 밸브 구조를 각각 타력식과 자력식으로 보면,
- 타력식 : 스템 선형 슬라이딩 밸브 – 게이트밸브, 글로브밸브, 다이아후람밸브 등
- 스템 회전 밸브 – 버터후라이밸브, 볼밸브, 프러그밸브 등
- 자력식 : 디스크 회전 운동형 – 스윙체크밸브, 틸팅디스크 체크밸브 등
- 디스크 상하 운동형 – 레귤레이팅밸브, 안전밸브, 릴리이프밸브 등
- 디스크 축선 운동형 – 노즐 체크밸브 등
밸브를 구조적으로 안전하게 압력을 유지시키면서 밸브 기능을 수행하기 위하여, 밸브 몸체와 본닛의 기계적인 체결 방법으로 구분하면,
- 볼팅 체결 방식(Bolted Bonnet type)
- 압력 밀봉 체결 방식(Pressure Sealed Bonnet type)
- 유니온 본닛 체결 방식(Union Bonnet type)
- 스크류 본닛 체결 방식(Screwed Bonnet type)
- 몸체 일체형(본닛레스) 체결 방식(Bonnetless – Integral Bonnet type)
- 용접형 체결 방식(Welded Bonnet type)
밸브 구조를 구체적으로 이해하기 위해서는 밸브의 분류를 참고한다.
5. 밸브호칭 직경 및 압력
밸브의 크기를 판단하기 위해서는 밸브와 직접적으로 연결되는 파이프(배관)와 같은 호칭 직경을 쓰는 것이 통일성 측면에서 바람직하다. 파이프는 적용되는 설계 압력에 따라 그 두께가 달라져야 하므로, 세계적으로 가장 널리 사용되는 규격이 ASME 기준인 ASME B36.10M & B36.19M 규정이다. 파이프는 호칭 파이프 크기(Nominal Pipe Size, NPS)로 표시하며, 단위는 인치시스템에 준하였다. 따라서 표기는 2”의 경우 NPS 2로 표기한다. 다음의 그림 7에서 보는 것과 같이 NPS 1/8에서 NPS 12까지는 파이프 외경과 NPS는 일치하지 않고, NPS 14이상부터는 파이프 외경과 NPS가 일치한다. 예로 NPS 12의 경우, 파이프 외경은 12.75inch이지만, NPS 14의 경우에는 외경이 14inch가 된다. 파이프의 두께를 표시하는 일반적인 방법은 스케쥴(Schedule, SCH)로 표시하거나, 별도로 두께를 표시하기도 한다. 엔지니어는 스케쥴을 어림잡을 때, 파이프에 걸리는 설계압력을 파이프 재질의 허용응력의 비율로 하여 대략 1000배를 곱하면 대략적인 스케쥴을 알 수 있다. 보다 구체적으로는 바로우 공식(Barlow’s formula)을 사용하여
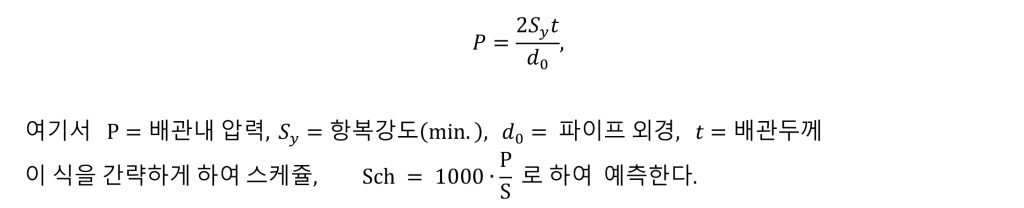
여기서 P = Design Pressure, S = Allowable Stress
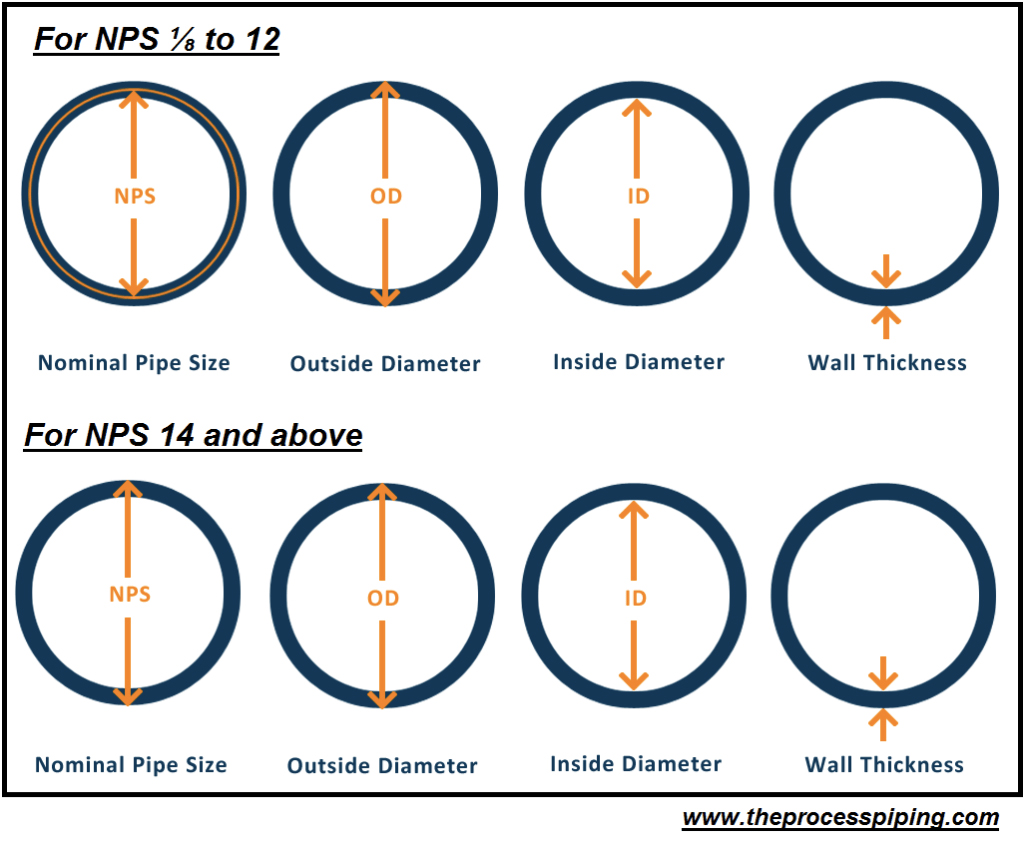
파이프의 NPS별 내, 외경 비교
유럽의 경우(국제표준)에는 ISO 6708에 따라서 DN(Diameter Nominal)으로 표기하며, 단위는 기본으로 mm이다. DN은 간혹 NB(Nominal Bore)로도 종종 표기한다. 단 DN 기준은 단순히 호칭 치수이므로, 구체적으로는 DN/OD 또는 DN/ID로 정확한 치수를 표현하여야 한다.
밸브의 호칭 직경에 관한 기준은 파이프와 같으나, 이는 파이프에 연결되는 밸브의 입∙출구 노즐단이 파이프의 호칭 치수와 맞아야 하기 때문이다. 다음의 표 2는 NPS와 DN의 관계를 보여준다.
밸브 설계에서 밸브 포트의 내경을 정하는 것은 전적으로 밸브 설계자의 판단이지만, 밸브 포트의 직경이 제작자마다 다를 경우, 사용자는 큰 혼란을 가질 수밖에 없다. 따라서 AMSE B16.34에서는 이에 대한 가이드 라인으로 파이프 사이즈(NPS)와 내경과의 관계를 임의 부록 A로 규정하였다. 임의 부록 A는 ASME B16.5 플랜지 피팅의 내경 기준으로 플랜지 접속단 밸브 뿐 만 아니라 용접단 밸브의 내경을 결정하는데 지침이 될 수 있다. 저압등급의 경우 NPS가 24인치를 넘는 것과, 고압 등급인 ASME 2500이상의 경우에는 NPS가 12인치를 초과하는 경우에는 모두 선형 외삽법(Extrapolating Method)을 통하여 내경을 산출하였다. 다음 표 3은 파이프 사이즈와 밸브의 기준 내경(포트 직경)을 보여준다.
통상적으로 표 3의 밸브 포트 직경은 파이핑에 있어서 실질적인 100%의 유로 직경을 갖는 것이기 때문에 이 값의 90%이상이면, 관습적으로 풀 포트(Full Port)라고 하고, 90% 미만이면 레듀스드 포트(Reduced Port)라고 한다. 그러나 초임계압 이상의 고온 과열 증기인 경우, 유속을 100m/sec이상으로 할 수 있기 때문에, 고객이 비록 풀 포트를 요구한다 하여도 과열증기 시스템인 경우 표 2의 기준에 90% 이하의 포트 직경의 밸브(단 개폐용도의)도 실제 현장에서는 종종 허용된다. 증기 플랜트의 엔지니어링 측면에서 과열증기인 경우, 밸브 포트 직경을 ASME B16.34 Table A의 값에80~85%로 포트 직경을 잡아도 전체 시스템에 미치는 밸브에서의 압력 손실의 영향은 미미하다 할 수 있다.

배관 호칭 직경 – DN과 NPS
파이프가 설계압력에 대하여 스케쥴로 표시되는 파이프의 두께라고 하면, 밸브의 경우에는 ASME B16.34에서 규정한 압력-온도 기준(Pressure-Temperature Ratings)이 된다. 즉, 압력등급은 해당되는 설계온도에서 안전 여유를 충분히 가진 해당 재료의 강도에서 설계(사용 가능한)압력을 나눈 값으로 Class 150부터 Class 4500까지가 ASME B16.34에 규정되어 있다. 즉,


ASME B16.34에서 정하고 있는 밸브 내경
반면에 유럽의 경우에는 PN(Pressure Nominal)로 표시한다. 이는 좀 더 간단하고 직관적으로, 상온에서 밸브가 견딜 수 있는 압력을 bar 단위의 압력으로 표시한 것으로, 사용온도가 높아지면 재료의 허용응력이 낮아짐으로 적용압력은 낮은 압력이 된다. 예를 들면, PN40은 상온에서 40barg의 압력까지 사용 가능하지만, 밸브 사용온도가 300도로 높아지면, 재질에 따라 다르겠지만 적용 가능한 압력이 30barg이하로 떨어진다. 예로써, API에서는 ASME/API와 PN과의 관계를 다음과 같이 정하였다.
⎯ PN 20 (ASME class 150)
– PN 50 (ASME class 300)
⎯ PN 64 (ASME class 400)
⎯ PN 100 (ASME class 600)
– PN 150 (ASME class 900)
⎯ PN 250 (ASME class 1500)
⎯ PN 420 (ASME class 2500)
6. 배관접속단구성
밸브는 주로 파이프와 접속하여 배관 시스템을 구성한다. 밸브와 파이프 간의 접속부 형상은 밸브에 있어서 매우 중요한 부분이다. 밸브를 호칭할 때, 사이즈와 호칭 압력의 다음에 접속부의 형상을 필히 호칭한다. 그 이유는 접속부의 형상이 배관 시스템의 성격에 따라 각기 다르고, 온도와 압력, 그리고 밸브의 운전 편이성에 더하여 유체의 성질에 따라서도 밸브 접속부 형상은 달라지기 때문이다. 일반적으로 많이 사용되는 밸브의 접속부 형상은 주로 다음과 같으나 이 외의 특수한 형상도 점차 많이 적용되고 있다.
- 나사형 체결구조(Threaded Ends) : NPT, PT, 유니온 체결(Union Joint)
- ASME B1.20.1(NPT, 미국 파이프 나사 규격), ASME B16.11(단조 피팅)
- 플랜지형 체결(Flanged Ends) : Flat Facing(FF), Raised Facing(RF), Ring Joint (RTJ), Male & Female Face, Tongue Face, Groove Face 등이 있다. 관련 코드와 기준 : ASME B16.5, MSS SP-6
- 용접형 체결(Welding Ends) : Butt Weld(BW), Socket Weld(SW)
- ASME B16.25(BW), ASME B16.11(단조 피팅, SW)
- 경납땜 체결 – 주로 냉난방, 공조 기기에 쓰이고, 플랜트 산업에서는 드물게 사용됨
- 메카니칼 조인트(Mechanical Joints) : Grayloc, Techlok
전형적으로 메카니칼 조인트는 3개의 부품군으로 구성되며, 각각 두개의 허브(Hub), 클램프(체결 볼트 포함)와 허브 사이에서 외부로의 누설을 막아주는 금속재 씰링으로 구성되어 있다.
메카니칼 조인트는 몇몇 업체에서 독점적으로 취급하는 제품이어서, 아직까지는 산업 기준으로 정립이 되어 있지 않으나, 여러가지 사용상 잇점이 많기 때문에 점차 보편화 될 것으로 보인다. 따라서 향 후 가까운 싯점에서는 메카니칼 조인트에 대하여도 산업기준이 마련될 것으로 예상한다. 아래 그림은 메카니칼 조인트의 사용상 장점이다.
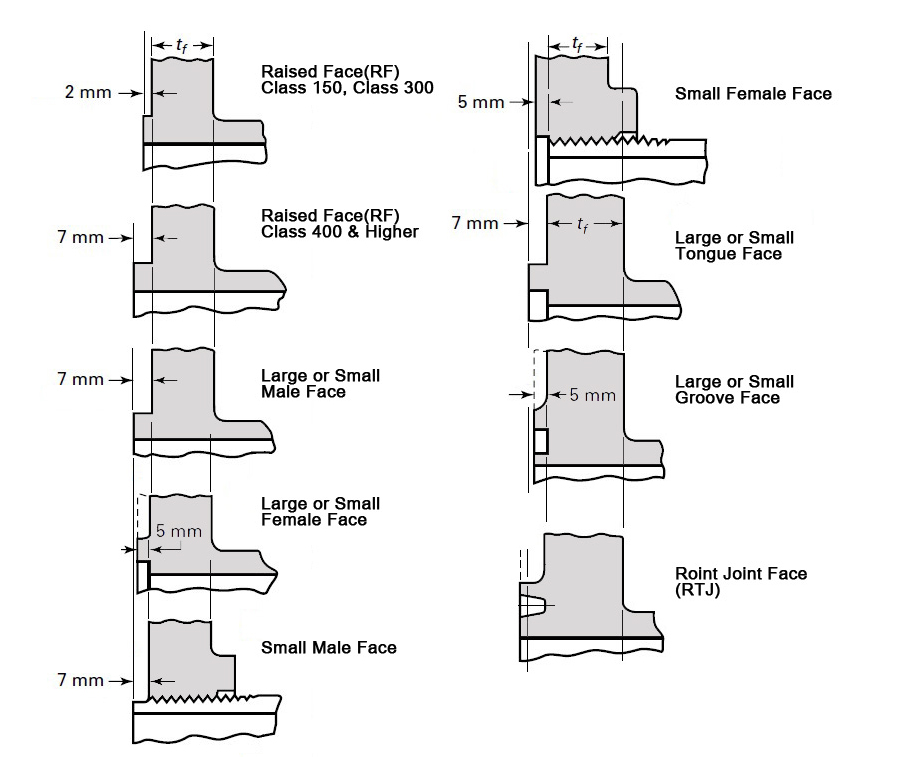
플랜지 접속단 형식
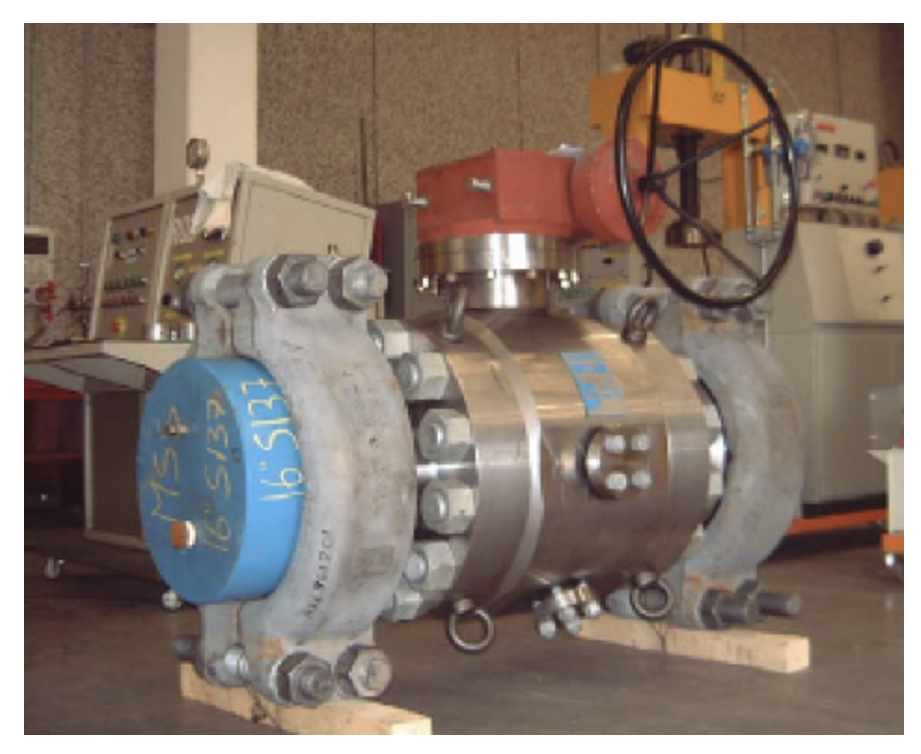
- 일반 플랜지보다 매우 경량이고 소형
- 체결 볼트가 소량으로 용이한 체결 구조
- 유지보수가 용이하고, 소프트 가스킷이 없어 사용 중 다시 조일 필요가 없음
- 금속 씰은 파이프내의 압력에 의해 씰 기능을 보완하는 포지티브 씰링 구조
- 산업 기준/표준이 없는 독점적 제품으로 Grayloc & Techlok등의 상표가 있음
- 금속 씰 부분의 가공 정밀도가 요구됨
- 제조사가 제시, 공급하는 메카니칼 조인트와 완전 호환되어야 함.
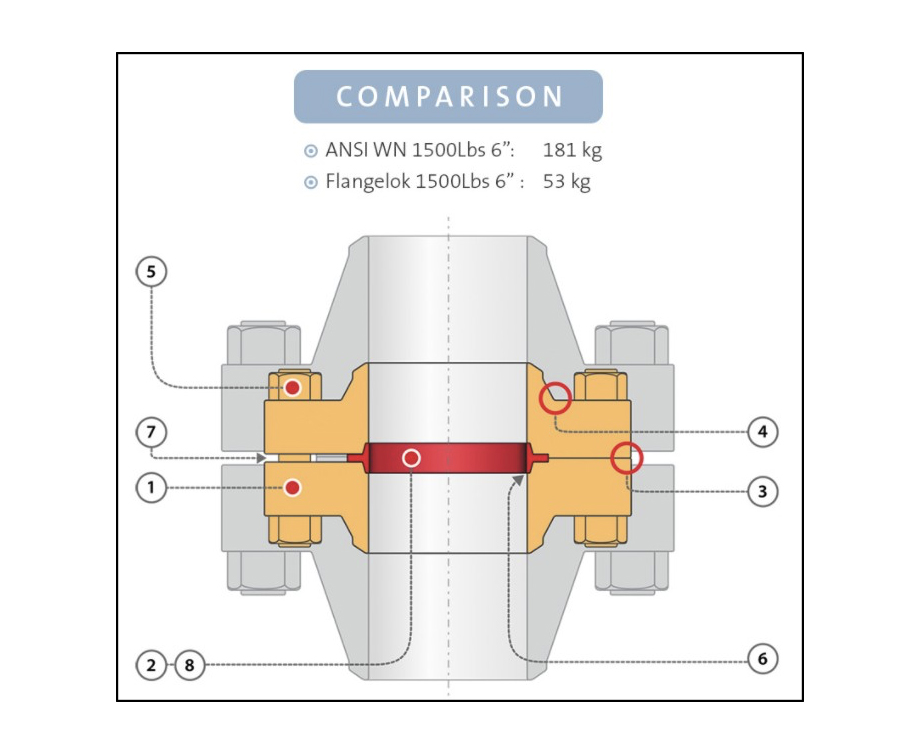
- 동등 플랜지에 비하여 무게와 공간의 대폭적인 절약으로 경제성 확보
- 고온고압에서의 완벽한 무용접 씰링
- 배관설계 및 시스템 운전측면에서 편이성 극대화
- 기존 플랜지 볼트 체결 노력에 비하여 25%이하의 체결노력 – 큰 사이즈의 경우 10% 이하도 가능
- 최고 효율의 유체 흐름 유로의 구조 구현
- 분해 및 조립의 용이성 극대화
- 금속제 씰링의 다양한 선택이 가능
8. 밸브주요재료
밸브의 제조에 쓰이는 재료는 밸브의 용도가 워낙 다양하고, 또한 사용 유체의 성상과 사용 환경에 따라 부식이나, 침식 또는 사용 유체와의 화학적 반응의 문제로부터 오염의 문제까지도 크게 영향을 받기 때문에 다양한 재료가 쓰일 수밖에 없다. 전형적인 극한 서비스 용도인 우주개발용 밸브의 경우에는 극한의 저온과 고온에 각각 견디어야 하고(예로서, Space X사의 Starship의 Raptor 로켓 엔진 연료조절의 밸브의 경우 초고압(643barg), 극저온(-183℃)의 액화 메탄 가스와 액화 산소를, 엔진 가동시에는 1500도를 넘는 극한의 고온에 견뎌야 함), 보편화된 최근의 액화 천연가스의 경우에도 항상 -163도의 초저온 상태에서 운전되어야 한다. 이 책에서는 산업용 프로세스 밸브만을 대상으로 하기 때문에 이러한 특수 운전조건하의 밸브를 다루기에는 한계가 있다.
산업용 밸브를 구성하는 재료는 일반적으로 밸브의 압력 유지 부품으로서 밸브의 구조적 안전성을 담보하는 밸브 몸체와 본닛, 이를 구조적으로 연결하는 본닛 볼트를 (1) 기본 재료로 하고, 실질적으로 유체와 접촉하면서 밸브의 본 기능인 유체 제어 기능을 수행하는 밸브 디스크, 프러그, 시트, 케이지, 스템 등과 같은 트림부품에 쓰이는 재료를 (2) 중요 부품 재료라고 한다. 그리고 이들 내압을 받는 압력 유지 부품과 밸브의 제어 기능을 수행하는 중요 부품을 구조적으로 건전하게 유지하며 밸브 운전을 안정적으로 도모하는 패킹과 가스킷은 물론 요크와 슬리브 등, 기타의 밸브 구조물들의 재료들을 (3) 기타 밸브 구조 재료라고 한다. 모든 밸브 재료는 제조의 용이성, 기계적 강도 특성과 화학적 적합성, 기계 가공 및 용접의 편이성은 물론 소재 확보의 안정성과 경제성이 함께 검토되어야 할 것이다.
9. 밸브의 검사
밸브의 검사는 밸브의 종류, 사용조건 및 목적에 따라 검사 방법 또한 상이하지만, 일반적으로 수행하는 검사와 특정 목적에 맞춰서 하는 특수검사 등을 한데 합하면 대략 다음과 같다. 밸브 검사에 대한 구체적인 사항은 제10장 밸브 응용사례에서 구체적으로 설명한다. 특별히 밸브 검사 및 시험항목 중, 비파괴검사는 특별한 전문성이 요구되고, 제3자에 의한 객관적이고 독립적인 검사가 필요한 관계로 밸브 제작사는 전문 검사기관에 이들 비파괴검사업무를 의뢰하여 수행하는 경우가 매우 많다.
- 재료검사 – Material Test Certificate
- 외관검사 – Visual Inspection Test Report
- 비파괴검사 – Non-Destructive Test Certificates
- 치수검사 – Dimension Inspection Test Certificate
- 조립검사(기능검사) – Functional Test Certificate
- 수압검사 – Hydrostatic(Shell) Test Certificate
- 시트기밀검사 – Seat Leakage Test Certificate
- 백시트 기밀검사 – Back Seat Leakage Test Certificate
- 특수검사 – Special Test
- 증기시험(Steam Test)
- 저온검사(액화가스 등 저온 유체일 경우)
- 유량특성검사(유체 흐름에 대한 밸브의 제반 특성을 검사)
- 내화특성검사(Fire Safe Test – 화염에 대한 밸브의 제반 성능을 검사)
- 밸브 파괴검사 – 일종의 밸브 몸체의 강도시험으로 어느 부위, 어느 정도의 힘에 의해 밸브 구조강도가 손상을 입는가에 대한 검사
- 패킹과 가스킷 부의 유해물질 누설시험(Fugitive Emission Test)
10. 밸브 보수검사 – 검사 중 불합격 부분을 용접이나 기타의 방법으로 보수 또는 수정했을 때 수행하는 검사
10. 밸브규격의 개요
밸브의 규격은 밸브와 관련된 모든 사항 즉, 모든 사람들이 상호 이해할 수 있도록, 사용상의 안전이나 환경은 물론 호환성과 사용 목적의 적합성 등등을 표준화하여, 규격으로 제정하여 활용한다.
(1) | 상호 이해 | 용어, 기호, 양식 등의 통일은 물론 업무 절차의 일관성 |
(2) | 인간과 물자의 안전 | 안전, 건강, 환경의 건전한 유지 |
(3) | 공통성, 호환성 | 일관된 시스템 구현 |
(4) | 사용목적에의 적합성 | 제작 프로세스 및 제품의 품질과 성능 |
(5) | 일관화, 단순화 | 균일한 품질, 업무의 효율성 제고 |
이러한 기준 하에 규격을 만들고, 이를 철저하게 시행하면 기획에서부터 영업, 설계, 생산, 유통 및 소비에 이르기까지 업무의 단순화와 일관화로 품질 향상과 비용절감, 납기단축 및 고객서비스 향상에 이르기까지 유무형의 효과가 기대된다.
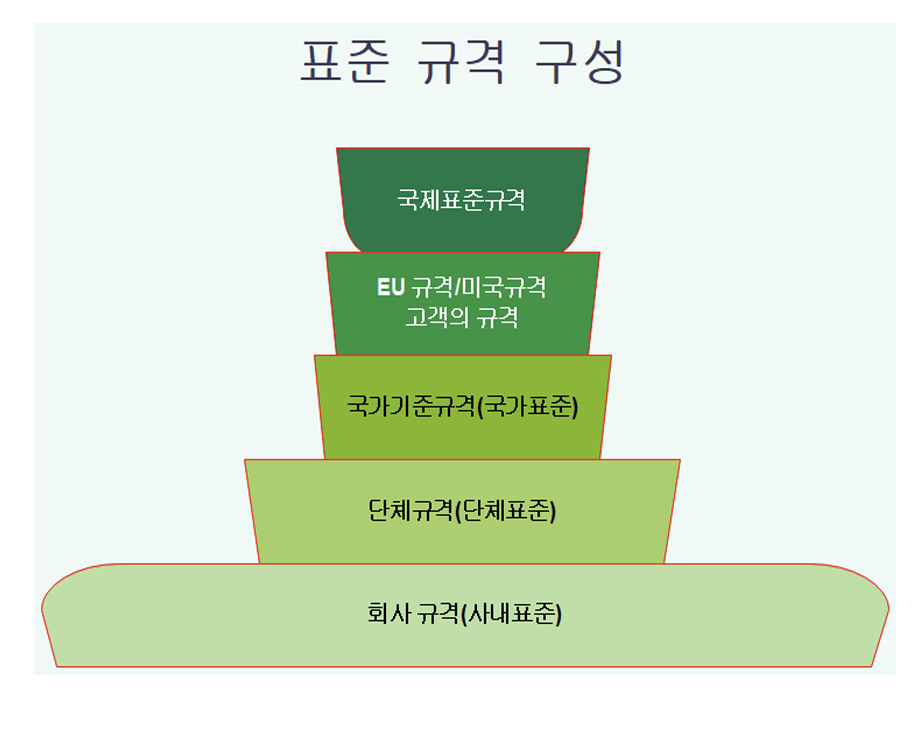
표준 규격 구성은 최상위의 국제표준부터 최하위인 사내 규격까지 적어도 5단계 이나, 가장 널리 쓰이는 미국 국가규격의 경우, 단체 규격이 국가 표준으로 등재 하는 경우가 많아 표준 규격의 피라미드 와는 차이가 있다. 또한 발주자인 고객의 요구사항은 계약 상의 상위단계에 있는 경우도 많기 때문에 일반적 으로 회사 규격은 산업권역별(EU 또는 미국)로 구분 하여 별도로 유지하는 경우도 있다.
밸브의 규격과 관련하여서는 국가의 규격(또는 표준)으로 5-(9)의적용 산업 표준(Codes) 및 기준(Standards)에 의한 분류를 참고한다.
11. 밸브의 선정
밸브를 구입할 때, 사용자는 사용상의 목적에 맞는 적절한 밸브를 선정하고, 여기에 꼭 필요한 사항들을 밸브 제작자에게 문서(구매사양서, 구매 기술사양서, 밸브 데이타 시트 등)로 요청한다.
밸브 제작자는 구매 문서에 기준하여 밸브 사양을 결정하고, 설계 및 제작에 따른 후속 프로세스를 진행한다. 밸브의 올바른 선정은 제작자 또는 구매자 어느 일방의 책임이 아니라 공동의 책임이라는 의식하에 사용목적에 비교하여 너무 고급 사양이거나 사용 목적과 동 떨어진 사양이라면, 서로 의견(주로 사양변경 요청서 – Deviation Request 등)을 교환하여 서로에게 가장 좋은 품질의 적정한 가격의 밸브로 선정하는 것이다. 그러나 다음과 같은 사항들은 견적 단계 또는 수주 후 기술협의 단계에서 중요하게 논의되어야 할 내용들이다.
- 시스템과 관련 법규에 맞는 밸브 선정인가?
- 유체의 압력, 온도는 물론 밸브 설치에 있어서 연계 배관계통 또는 연계기기와의 강도 평형(Strength Balance)을 충분하게 고려했는가?
- 배관계통의 히트 평형도(Heat Balance)에 밸브 자체의 압력 손실량 또는 유량계수가 합당한 능력을 갖고 있는가?
- 연계 배관과의 접속방식은 일치하는가?
- 유체의 제어목적에 적합한 기능을 갖고 있는가?
- 밸브의 조작방법은 유체 제어목적과 기능상 일치하는가?
- 유량 조건에 적합한 구조와 용량을 가진 밸브인가?
- 유체 성상의 특성에 맞는 밸브 재질인가? 적용상의 제한사항은 없는 밸브 재질인가?
- 밸브 사용빈도에 적합한 밸브인가? 특히 사용빈도가 매우 낮을 경우 보수 및 작동불량에 대한 대책은 수립되어 있는가?
- 밸브 설치 위치 및 방향은 밸브 운전 및 고유 성능에 영향을 줄 수 있는가?
- 밸브의 부식방지 대책은 설치 환경에 부합하는가? 설치 환경에 따라 습도, 온도의 급격한 변화, 미세한 오염물질의 유입 여부 및 유해 휘발성 유기물의 법적인 규제 등은 사전 면밀하게 검토되어야 한다.
- 밸브 유지 보수 및 운전환경은 충분히 고려되었는가?
- 고에너지 밸브의 경우, 밸브의 피로 수명에 대한 요구사항은? 피로수명 평가 보고서를 설계에 반영하고, 입증하여야 하는가?
12. 밸브취급상유의사항
(1)배관 설계 시
- 밸브는 시스템에서 요구하는 기능을 발휘하여야 하므로 가급적 접근하기 쉽고 관리하기 쉬운 장소에 설치하도록 해야 한다.
- 밸브는 특별한 사유가 없는 한 밸브 스템이 수직이 되도록 설치하고, 자력식 밸브의 경우에는 수평 배관라인에 설치하는 것이 좋다. 또한 밸브 조작과 정비 보수가 용이하도록 적당한 조작 및 보수 정비 공간을 확보하여야 한다.
- 긴급 조작이 필요한 밸브의 경우에는 접근 통로가 안전하게 확보된 곳에 밸브를 설치한다.
- 밸브의 자체 무게 또는 구동장치의 무게 중심이 높은 경우, 조작력에 의한 밸브 구조에 무리가 가지 않도록 밸브 또는 배관에 지지대 설치를 고려해야 한다.
- 밸브는 배관계통의 팽창, 수축, 진동이나 기초 지반의 침하로 인하여 밸브와 배관의 연결단에 무리한 집중 하중을 받지 않도록 배관 설계 시 이를 고려해야 한다.
- 밸브가 펌프와 같은 진동 유발 기기와 가까이 있거나, 유체 천이가 일어날 수 있는 유체 제어기기의 운전과 함께 운전해야 할 경우, 진동 또는 이로 인한 공진이 유발될 수 있어, 이를 고려한 밸브 설치 위치가 결정되어야 하고, 밸브 또는 배관에 지지대 추가 설치를 고려해야 한다.
(2)운반 및 보관
- 밸브를 설치 또는 운반 시 안전한 운반이 도모되어야 한다. 포장이 훼손되어서는 안된다.
- 보관 장소는 먼지와 온도- 습도를 관리할 수 있는 청결한 곳이어야 한다.
- 밸브 접속부는 어떤 외부의 충격이나 이물질의 유입이 없도록 확실하게 보호되어야 한다.
- 운반 및 보관 시에는 밸브에 어떠한 조작도 금지한다.
- 영하 10도 이하의 저온이나, 40도 이상의 고온, 다습 또는 진동이 있는 장소에는 절대 방치 보관해서는 안 된다.
(3)설치
- 밸브 설치는 사전 밸브 태그 번호를 필히 확인한 다음에 설치 장소로 운반한다.
- 설치에 필요한 제반 부품(가스킷, 볼트, 너트, 씰링용 용재 등)과 체결 도구를 준비하고, 용접이 필요한 경우, 용접봉 재질이 배관과 밸브 재질에 맞는가를 재차 확인한 후에 설치한다.
- 연결 접속부를 청결하게 하고, 용접시에는 인증된 용접절차에 따라 용접 설치한다.
- 밸브는 유체 흐름의 방향이 정해져 있음으로 이를 확인하여 배관의 유체 흐름 방향과 일치하게 설치한다.
- 밸브를 들어 올려 배관의 중심과 밸브 유로 중심을 정확하게 맞추기 위해서는 적어도 2~3개의 위치 조정장치를 사용하여야 한다.
(4)배관의 산세(酸洗) 크리닝 및 증기 블로잉(Steam Blowing)
- 밸브의 시트 기밀 유지를 보증하기 위해서는 배관 내부는 어떠한 이물질이 남아 있지 않도록 필요한 화학적 세정과 더불어 압축 공기 또는 증기를 사용하여 청결하게 하여야 한다.
(5)밸브의 조작
- 무리한 조작 또는 오 조작 금지 : 필요이상의 과도한 힘으로 밸브 조작을 하게 되면 밸브의 시트 구조 또는 스템에 영향을 주어 시트 누설이 발생할 수 있다. 밸브의 형태나 기능에 따라 조작방법이 다를 수 있으므로 주의하여야 한다. 긴급 또는 비정상적인 상황인 경우, 밸브 조작은 지정된 책임자에 의해서만 조작되도록 해야 한다.
(6)밸브 운전 보수관리
밸브의 운전 보수관리 세부사항은 제조사의 밸브 운전 및 정비 보수 매뉴얼의 절차에 따르고 여기서는 일반적 수준의 사항만을 기술한다.
그랜드 패킹의 누설
- 배관시스템의 수압시험(내압시험) 검사 및 시운전 시의 그랜드 패킹에서의 누설은 특히 주의하여야 하고, 평상 시의 운전 시에도 그랜드 패킹의 누설 여부는 늘 점검하여야 한다.
- 누설이 발생하면 그랜드 볼트를 조여 누설 차단 여부를 확인하고, 계속 누설이 진행되면 패킹의 교체가 필요하다. 단, 운전 중인 밸브에서의 스템 패킹 누설은 밸브의 형태 및 개폐 운전 여부에 따라 조치 방법을 달리하여야 한다. 게이트 밸브의 경우, 개방된 상태로 운전하는 경우에는 밸브 스템을 완전히 백시팅한 후에 신규 패킹을 교체하거나 추가의 패킹을 삽입하여 조치를 행할 수 있으나, 유량을 조절하는 밸브의 경우에는 내압이 걸려있어 이러한 임시 조치가 불가능하다.
- 스템에서의 누설은 심각한 문제이므로, 가능한 한 신속하게 새로운 패킹으로 교체하여야 한다. 패킹 교체는 안전상 밸브 내부의 압력을 완전히 제거한 후에 작업하여야 한다.
가스킷에서의 누설
- 수압시험 시에 검사하여 이상이 없는 경우에 상시 검사보다는 정기적인 검사로 확인한다.
- 누설이 있는 경우에는 본닛 볼트 전체를 일일이 다시 균일하게 조여야 한다. 조임 토크는 각 볼트에 일정하게 하여야 한다. 가스킷 특성에 맞지 않는 무리한 체결력은 절대 금하여야 한다.
밸브 무빙 부품(Moving Parts)에서의 문제
- 스템의 나사부, 요크 슬리이브, 그랜드 패킹 부분, 그랜드 플랜지 볼트의 나사부분에는 주기적인 윤활 여부 등을 확인하여야 한다.
- 구동장치가 있는 경우에는 구동장치의 샤프트와 스템의 연결부(Connector) 체결볼트의 이완 여부를 주기적으로 확인하여야 한다.
시트 누설
- 시트의 기밀은 시운전 시, 일상 운전 시에도 항상 점검이 필요한 밸브의 핵심기능이다.
- 누설이 발생되면, 가능한 한 조속히 밸브를 분해하고 필요한 조치를 해야 한다.
- 누설이 발생한다고 밸브를 무리하게 닫거나, 개폐동작을 반복해서는 안 된다.